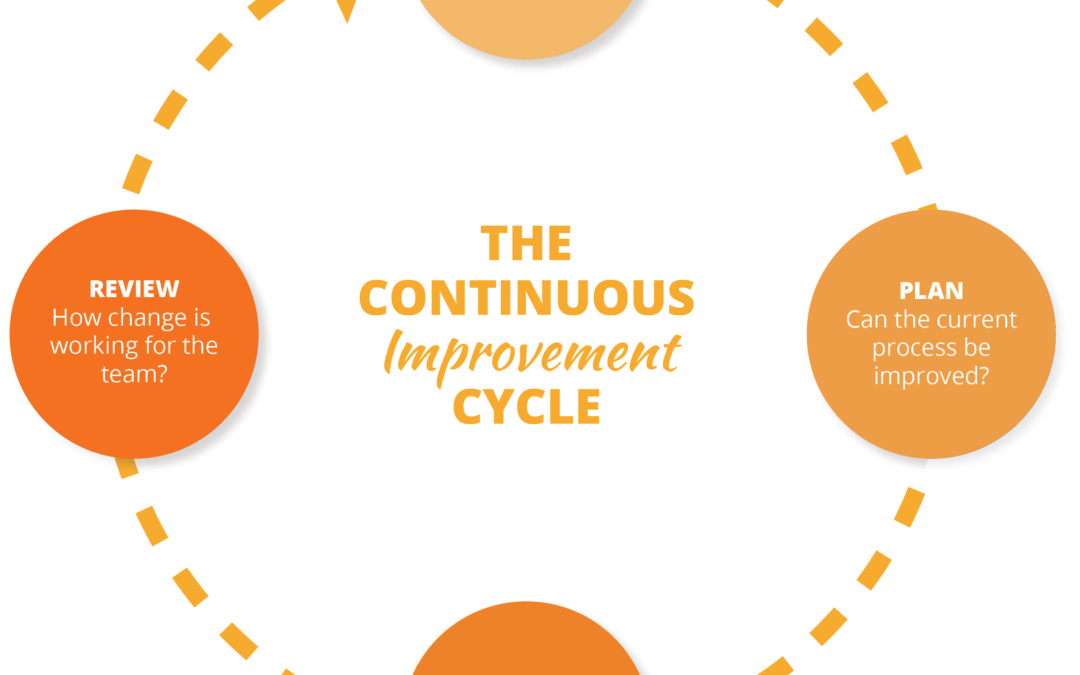
How to Foster Continuous Improvement
How to Foster Continuous Improvement
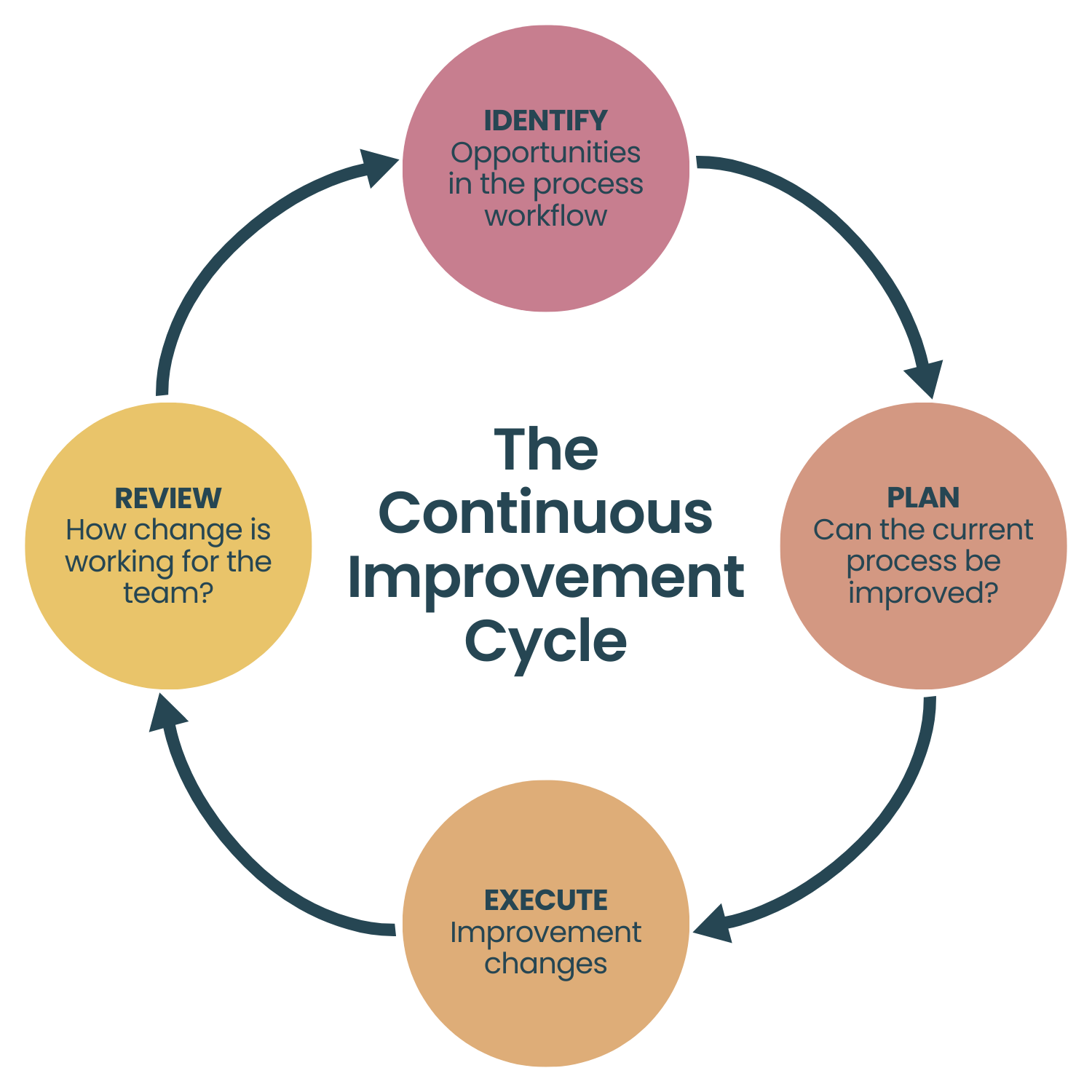
Continuous improvement identifies opportunities to reduce waste and streamline work. Broadly speaking, it finds opportunities to execute processes more effectively and get more from less.
Although this approach originated in manufacturing, continuous improvement is an essential element to countless successful companies across every conceivable vertical.
For many, there’s little doubt that fostering continuous improvement can drive sustainable, long-term results. The bigger question is often whether it be introduced effectively across all levels of their organization.
How individual staff can foster continuous improvement
As individuals within an organization, staff can encourage and support continuous improvement while also enjoying its benefits. As individuals within an organization, staff can encourage and support continuous improvement while also enjoying its benefits.
The Kaizen process is the almost synonymous methodology for this. The term itself translates to “continuous improvement” in Japanese.
Popularised by Toyota, Kaizen focuses on making small, frequent improvements to existing processes, and from any level of an organization. Kaizen challenges stubborn “how we’ve always done things” attitudes typically found in well-established organizations. By way of making micro-changes, Kaizen eliminates waste and silos. It aims for standardised processes in:
Quality of products, business processes and following best practices
- Cost of resources
- Delivery time and non-value-added activities
- Management of attitudes, training, flow and documentation
- Safe working conditions
Individuals can implement the Kaizen philosophy by:
- Using flowcharts or value stream maps to visualize current processes and identify areas of improvement.
- Questioning the status quo in order to make meaningful changes to processes.
- Dropping the pursuit of perfection – no methodology can ever create perfect systems or processes, but they can continuously improve conditions.
- Celebrating your successes and those of your team members in small ways to keep everyone invested and engaged.
- Setting aside time for team collaboration on improvement projects.
How leadership can foster continuous Process Improvement through systems & culture
Leadership have an equally important role to play as front-line staff. They can often contribute large amounts through creating a change culture.
This can be done by:
- Empowering everyone to make small changes in their own processes. Small ideas can lead to big changes.
- Creating an environment where employees feel free to address problems and pitch ideas. If the idea doesn’t work out, it should be iterated and improved instead of dismissed as a failure.
- Holding continuous improvement events, providing team members with tasks to action to help new processes take hold within the organization.
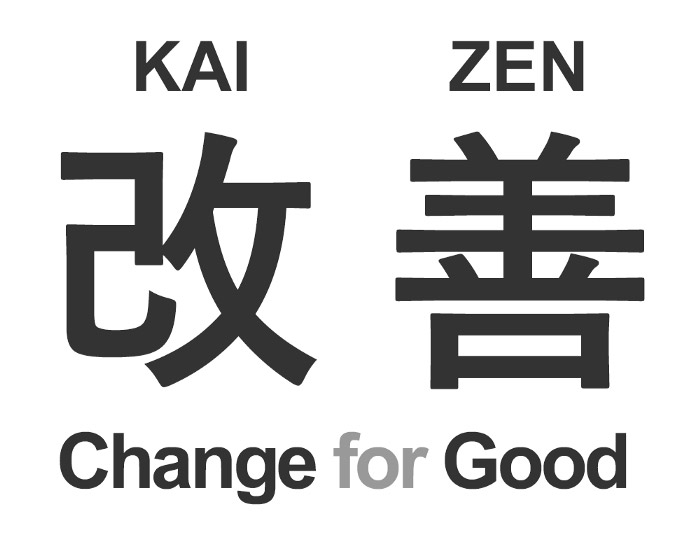
While Kaizen can be highly applicable on a company-wide scale, Total Quality Management (TQM) is a methodology that leaders may wish to utilize or borrow from. Gaining popularity in the late 1980’s after the US Federal Government implemented it, TQM strives for customer satisfaction.
Organizations using TQM typically adhere to the following principles:
- A strategic and systematic approach should be followed.
- Customers determine the quality level.
- Employees are to work towards common goals with effective communication and training ensuring consistent quality.
- Organizations should define the steps that are required in any process and monitor performance, continuously looking for ways to compete.
Diagrams are readily embraced by TQM companies, including Ishikawa diagrams, flowcharts and check sheets.
Aside from these systemic efforts, company leaders also need to make changes to culture to support continuous improvement by:
- Recognizing and rewarding continuous improvement successes, such as with raises, promotions, bonuses or even recognition.
- Becoming a courageous change leader by supporting constructive disruption.
- Leading by example, such as by being receptive to feedback or conducting regular self-assessments with vulnerability.
- Thinking of ways to develop your employees, not just your product or service.
- Hiring with diversity in mind in order to benefit from a broad spectrum of perspectives and ideas.
How individual staff and leadership can work together to foster continuous process improvement
A culture of continuous process improvement can only thrive if individual staff and leadership work together.
Continuous improvement should be integrated into all aspects of the business. For example it can be included in internal communication, KPIs, personal development programs and job descriptions.
A shared vision needs to be emphasised through these everyday activities, reiterating the need to strive towards a common goal.
A suggestion process should be developed so that ideas can be easily gathered and evaluated. This also includes developing a clear system to follow instead of allowing individuals to implement changes at will.
Collaboration on continuous process improvement needs to be done through empowerment, involvement and suggestions, not directions or orders.
As well as improving production and costs, continuous process improvement improves morale and satisfaction, leading to better outcomes and retention.
Small changes can make an enormous difference, with a thriving continuous improvement process setting you up for sustainable success.