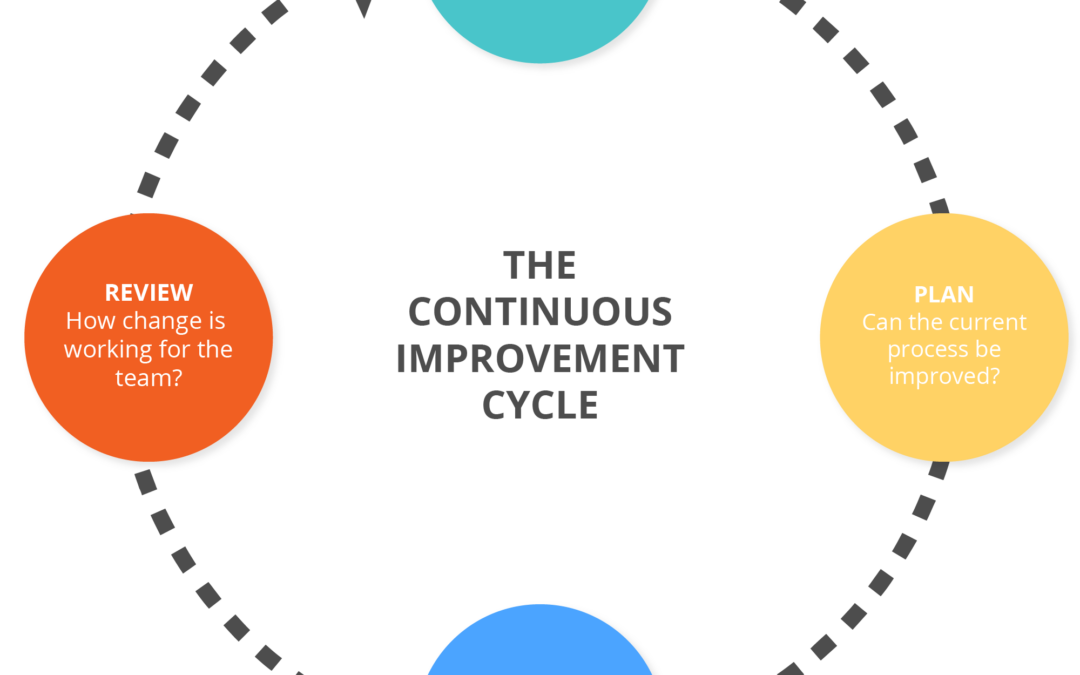
What is Lean Process Improvement?
What is Lean Process Improvement?
Looking for a way to make sense of the complex parts of your organization? Know there are error-prone areas in your business? Wish there was a way to provide more clarity to your employees so they can be more productive? If you’ve answered yes to any of these, lean process improvement could be just what you need.
What is Lean Process Improvement?
Lean process improvement is a user-centric commitment to continually trim excess from an organization’s operations. From its origins in the Japanese manufacturing sector of the 1950s, lean process improvement is an approach that’s heavily geared around maximizing the productivity of people and the processes they power.
Improved customer experience should be one of the ultimate outcomes of lean process improvement – either directly or indirectly. If the proposed changes will not make a noticeable difference for the customer, there is no business case for undertaking such an initiative.
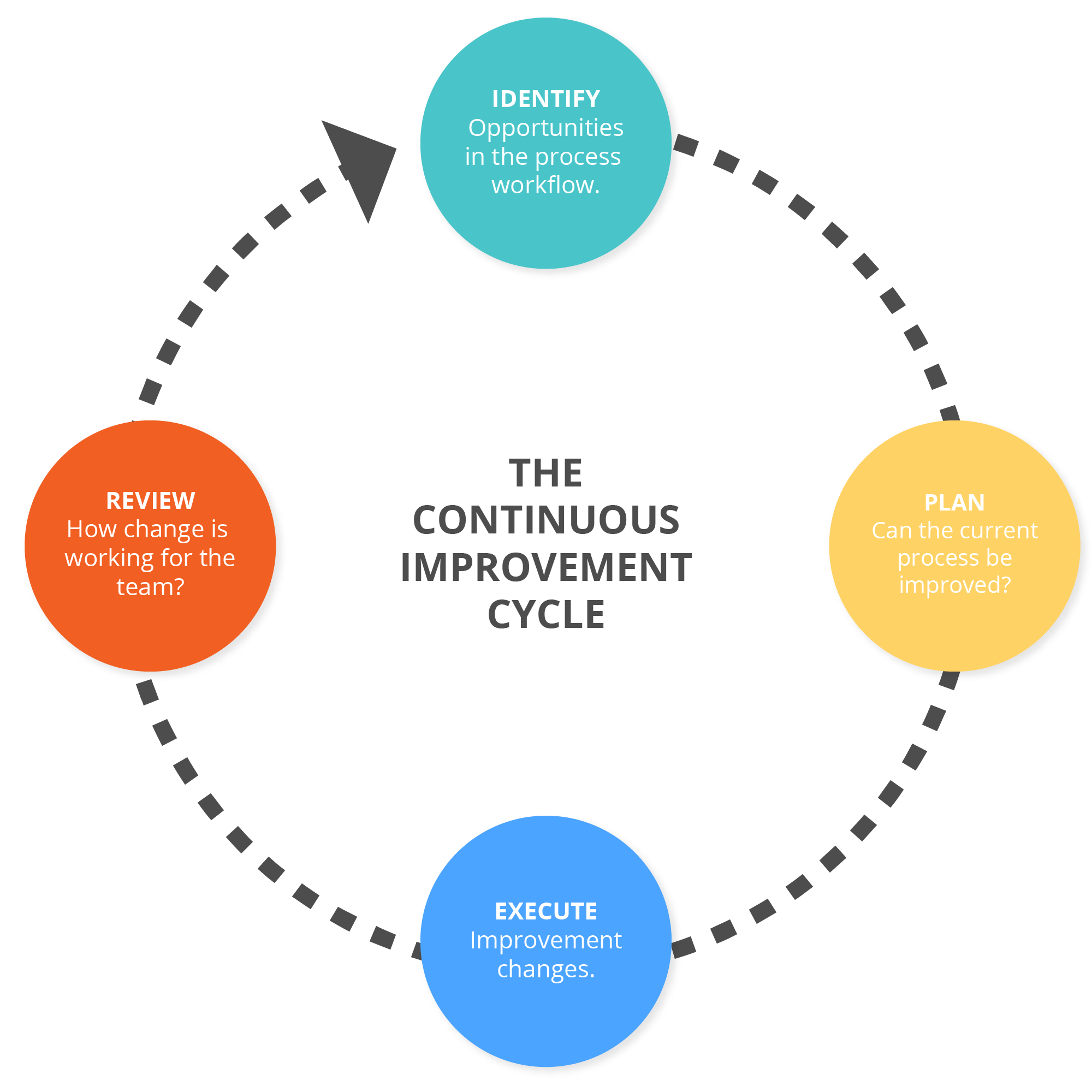
What are the benefits of Lean Process Improvement?
There are two types of benefits regarding lean process improvement. The first type broadly fits under the umbrella of improving business efficiency. It does this by:
Reducing excess
By eliminating wasted time or errors in a process, companies can either do more with the same amount of resources or can divert the cost savings to grow another area of the business.
Delivering value faster
Trimming the unessential processes of a business can shorten the time taken to accomplish a task – increasing its cost-effectiveness and scalability.
The second type of benefit that lean process improvement offers is lifting the overall retention of businesses. The key aspects of this are:
Improving employee morale
Any form of ambiguity or lack of clarity around business process can negatively impact an employee’s productivity. Having well-defined processes helps negates this. This added clarity provides a roadmap to follow. So when employees deliver from an operational perspective, they’re more satisfied. And if they’re more satisfied, they’re less likely to be tempted by the greener grass at other businesses.
Improving customer satisfaction
Unfortunately for businesses, customers seem to have a sixth sense when it comes to broken processes. Their high expectations mean that any hint of friction is often magnified, and thanks to the competitive environments most companies compete in, this means people can easily take their custom elsewhere.
But if you get your processes right and every part of your business is in harmony like a symphony orchestra, then your customers will be satisfied and stay with you long term.
What’s the best foundation for Lean Process Improvement software?
Processes often start out simple, but they can easily blow out and be very difficult to keep track of once established. Business process management and workflow automation software is the answer. In order to get the best ROI when embracing lean process management, there are two vital elements a business needs to get right.
One process to rule them all
The most effective implementors of lean business process management software share one thing in common – their entire company buys into the approach. While individual departments can operate lean, they will eventually operate at cross purposes with others, and waste and excess will result.
It’s a way of working, not a project
The final key to implementing and maintaining effective lean business process management software is to understand the paradigm shift that it is a mindset, not a one-off endeavor to dot is and cross ts. Yes, there will be times employees or departments want to take shortcuts, but this will affect the whole business. This is where Workflow Automation software comes to the fore, as it enforces compliance organization-wide.
If lean process improvement is bought into by all employees all the time, the organization will in turn reap significant rewards.
Want to find out how going Lean can help you streamline your processes? Get your free demo of Flowingly today.